Everything in manufacturing is intentional, from the machines utilized to the processes and operations in production— and material is no exception. Medical device producers around the world use a variety of materials, but metals, polymers, and ceramic are the most popular materials for orthopedic implant manufacturing. When manufacturers decide upon what type of implant they want to produce, they first assess its intended purpose and verify that it will meet the patient’s needs. After making this determination, material selection follows suit. The type of implant needed is always directly correlated with the material used.
But looking beyond the active use of the implant, medical device producers have another factor to consider: manufacturability. Manufacturability refers to the ease of production and handling of an object or product. The term can apply to a wide variety of factors, from material content to simple functionality. There are several considerations that must be examined when determining whether a product is manufacturable in terms of both design and cost.
Orthopedic Implant Materials Selection
Manufacturing Polymer Orthopedic Implants
One of the most significant benefits of polymer components is that they help manufacturers produce excellent surface finishes during the molding process. This leads to superior optical properties when compared with metal parts cast onto a polymer substrate.
Manufacturing polymer orthopedic implants has a number of benefits, but this material also comes with its own set of unique limitations.
Pros
- Plastics generally have low melting points, allowing them to be molded into desired shapes easily
- Plastics can be colored before they are molded into their respective parts, minimizing the need for any post-machining painting and related secondary operations
- Plastics are very light in weight, which can be cost-saving by reducing shipping expense
Cons
- Since it has a low melting point, plastic does not fair well in high heat. If plastic materials are exposed to high temperatures, they have the potential to deform or warp.
- Compared to other materials such as metals and ceramics, plastics are less structurally supportive.
- Plastics are not found in nature, so they decay more slowly than other alternatives. This is not to say that the other material alternatives are good for the environment, but plastics are the most serious when environmental concerns are a priority.
- Polymers are relatively new to the industry, so there are still some unknowns about this material and its interactions with the body.
- Polymer orthopedic implants are designed with a specific patient in mind. They are typically made for those who experience knee pain after meniscus surgery but are too young for a total knee replacement.
Manufacturing Metal Orthopedic Implants
Perhaps the most common material for orthopedic implant production, metals are significantly more durable than plastics. Metals can tolerate more intense external forces than plastics can. At high temperatures where plastic would begin to melt, the metal stays strong. Metals are great thermal and electrical conductors and are typically easier to clean than plastics.
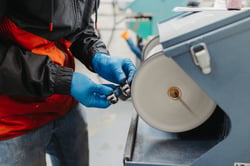
Manufacturers typically use Titanium and Stainless steel due to their unmatched strength-to-weight ratio compared to other metals, however promising developments in new alloys are now allowing manufacturers to tailor material characteristics even further to suit the application’s needs.
Like polymers, selecting metals as your orthopedic implant material of choice also has its own unique advantages and disadvantages.
Pros
- Metals are significantly more durable than plastics
- Metals can tolerate high temperatures and caustic environments
- Metals are great thermal and electrical conductors
- Metals are generally easier to clean than plastics
Cons
- Metals may require secondary operations such as finishing or painting
- Metal is typically used for geometrically simple pieces due to machining limitations
Manufacturing Ceramic Orthopedic Implants
Materials such as ceramics, while possessing desirable properties such as hardness, high temperature tolerance, and chemical resistance, also suffer from limitations such as limited design flexibility, lower strength, and brittle performance. For any given application, it may be necessary to combine ceramics with other materials such as titanium or polyethylene acetabular cups to provide optimal performance.
Ceramics have their own respective manufacturability pros and cons:
Pros
- Ceramics can tolerate high temperatures
- Ceramics demonstrate exceptional resistance to wear from exposure to highly aggressive chemicals
Cons
- Ceramics demonstrate high strength and can tolerate extreme physical stresses but only under optimal conditions.
- Ceramics have very limited design flexibility.
The Future Of Orthopedic Implant Materials
The current trend in orthopedic implants is moving toward more polymeric devices, but this does not mean that polymers are the perfect material. Even though they are biocompatible and often inexpensive, the material characteristics of polymers can be less than ideal. To compensate for their shortcomings, engineers frequently design implants that combine a metallic element with a polymer coating to improve performance.
It has been suggested that metals used in combination with biocompatible polymers exhibit better longevity of materials due to their superior properties over other materials used for implants. Metal-polymer composite implants typically have improved mechanical properties when compared with their pure metal counterparts. Polymers can act as insulation or lubrication, which improves the mechanical properties and reduces the risk of implant failure.
Metal-polymer composites are more expensive than simple metal components due to additional processing steps required during manufacturing. These steps can include secondary operations such as coating and finishing, which may increase costs, but produces a superior implant in biocompatibility and wear resistance. Composite materials also typically exhibit lower thermal conductivity than their pure metal counterparts, thus increasing the temperature resistance.
Design Considerations for Orthopedic Implant Material Selection
An implant’s design features and desired performance characteristics must be factored in when assessing the device’s manufacturability. Overall, manufacturers need to balance these tradeoffs with the available manufacturing capabilities during the design stage to produce an implant that will serve users’ needs.
The simplest way to balance manufacturability and design is by using a material that allows for minimal machining, has excellent mechanical properties, demonstrates both strength and flexibility, and enables complex geometries. At Micron, we apply decades of orthopedic implant manufacturing experience to help you make the right choice for your production needs. Our ISO 13485:2016 Certified, FDA Registered facility provides cutting-edge manufacturing services optimized for quality, cost, and efficiency.
Get in touch with Micron’s engineers today to learn how we can improve your orthopedic implant manufacturing operations.